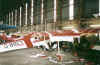 |
Removal of the
fabric whilst she is still in one piece allows photos of general assembly methods, cable
routings and some details to be pictured. This should hopefully assist in the
putting-back-together stage! Inside WWII T2 hangar at EGBG. |
 |
 |
A little more light is required
for some photos, so we drag her out for her last look at blue skies for a while.
Will those rib cap strips support flight?...perhaps only at Mach 1! |
 |
 |
Our group member, John Heard,
bless 'im, provided free transport to my house for the major components. That's me
on the right. Andy Duke on the left. John gets the free advertising in
exchange. |
 |
 |
Ensconced in my garage, 8'
wide, 32' long; a tight squeeze. Firewall removed from cowl, cleaned up &
Cleco'd back on to renew rivets. 1kW of lighting! |
 |
Fuselage condition
OK, no major corrosion found, but much previous repair work identified, and a few tubes
need straightening. |
|
 |
 |
New fairleads (10
required), use one of the original wire clips to hold it in place. 51/64"
outside diameter provides a nice snug fit. |
 |
 |
.....and
here are the finished articles. |
 |
 |
I decide to seal some tubes not
otherwise showing signs of having received previous
oiling efforts The far left photo shows a test of the re-sealing drive pin inserted in a test piece, to make sure I can
re-seal the hole. On the right here is the finished article. |
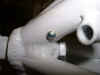 |
 |
I am using Pigeon
Poo (my colloquial term for "Duralac" barium chromate paste) to seal the drive
pinion. This paste is also very good for sealing rivets, screws, and any other
application where dissimilar metal corrosion may occur, and also between wood and metal
components. I will be using it to protect all my steel bolts through wood spars,
aluminium, etc. Available from Aeronautical or Nautical suppliers. Excellent
stuff. |
 |
Also going on is a
re-varnish of my beloved woodwork, after the Randolph one-part
varnish decides to react with the fabric cement after I tested it. So I purchase
some 2-part epoxy varnish from my local boat yard, sand off much of the old stuff, and
re-apply in 2-part epoxy varnish. An industrial sander works well here! I
think I'm up to the 150 hour mark on just the new door frames, but they'll be worth it. |
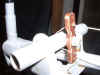 |
I remanufacture the
broken aft trim cable fairlead, using solid copper. The original was exemplary in
its lightness, but made of fibreboard with copper inserts must have been very expensive to
make, but bless CG for his attention to a light design. But I cannot afford the
tooling or time, so I have ventured for 1/16 oz extra weight and gone for the easy
option. I got the copper from an electrical supplier (it's a standard bus-bar
section).
Note: I have still not drilled the welded-up stabiliser holes in the cross-tube... |
 |
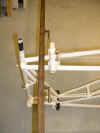 |
...because I am
still working with my alignment jig. Made from one long piece of random box section,
and one long piece (84") of 5/16 bar welded as one, which is then sawn at the
appropriate positions to fit into the stabiliser hinges. This ensures the 5/16 stubs
are in line, good and true. Photos will follow with it all fitted into the
stabilisers and made square and true with a similar fin/sternpost jig and the tailbrace
wires. |
 |
 |
3 views
of the shoulder harness attachment lugs welded into the cluster aft of the
headliner. Thank you Bruce for issuing the details in the Taylorcraft Owner's Club
Newsletter. The first two photos are viewed from vertically above. The third
photo is of the starboard attachment, viewed from the port side. Note the trim cable
string lines, no reason, just there!
The tube marked "FWD" in each case is the upper longeron.
I found that I had to modify the approved Taylorcraft drawing for the port (left)
side because the top diagonal tube got in the way of the hole. The first of these 3
photos shows this. Make cardboard templates first! |
|
 |